在現(xiàn)代電力傳輸與分配系統(tǒng)中,鋁合金電纜憑借其獨特的性能優(yōu)勢逐漸嶄露頭角,成為連接能源與用戶的重要紐帶。本文將深入剖析鋁合金電纜的制造工藝流程,并揭示其質(zhì)量控制的關(guān)鍵環(huán)節(jié),以期為行業(yè)內(nèi)外提供有價值的參考。
一、鋁合金電纜的制造工藝流程
1. 原料精選與準備
鋁合金電纜的制造始于對原材料的精挑細選。優(yōu)質(zhì)鋁錠、精確配比的中間合金及必要的添加劑共同構(gòu)成了電纜的基礎(chǔ)。在此階段,制造商需嚴格把控原料的純度與質(zhì)量,確保無雜質(zhì)混入,為后續(xù)工序奠定堅實基礎(chǔ)。同時,合理的儲存與運輸措施也至關(guān)重要,以防原料在流轉(zhuǎn)過程中受損。
2. 精密熔煉與合金化
原料經(jīng)預(yù)熱、加熱至熔融狀態(tài)后,進入保溫爐進行溫度均衡處理。隨后,中間合金與添加劑被精確加入,通過一系列復(fù)雜的物理化學(xué)反應(yīng),實現(xiàn)合金化過程。此階段,精煉與攪拌技術(shù)被廣泛應(yīng)用,以徹底去除鋁液中的雜質(zhì)與氣體,提升合金的純凈度與性能。
3. 連鑄連軋,塑造完美坯料
精煉后的鋁液在連鑄機中連續(xù)澆注成坯料,隨后進入連軋機組進行多道次軋制。通過精確控制軋制參數(shù),如軋制力、速度及冷卻條件,確保坯料具備優(yōu)異的力學(xué)性能與表面質(zhì)量。此步驟對于后續(xù)緊壓工藝至關(guān)重要。
4. 導(dǎo)體緊壓,提升導(dǎo)電性能
為彌補鋁合金在導(dǎo)電率上的不足,采用先進的緊壓工藝對導(dǎo)體進行極致壓縮。通過精心設(shè)計的模具與絞合設(shè)備,實現(xiàn)導(dǎo)體截面的最大化利用,顯著降低電纜外徑,同時提升導(dǎo)電性能與機械強度。
5. 退火處理,消除應(yīng)力
緊壓后的導(dǎo)體需經(jīng)歷退火處理,以消除加工過程中產(chǎn)生的內(nèi)應(yīng)力,進一步提升導(dǎo)電性能與穩(wěn)定性。退火溫度、時間與量的精確控制是此步驟的關(guān)鍵,需根據(jù)合金特性與工藝要求精心設(shè)定。
6. 鎧裝與護套,構(gòu)筑堅固防線
最后,退火后的導(dǎo)體被包裹以特殊設(shè)計的鋁合金帶聯(lián)鎖鎧裝層,形成一道堅不可摧的防護屏障。隨后,外層護套的添加更是為電纜提供了全方位的保護,確保其在各種惡劣環(huán)境下均能穩(wěn)定運行。
二、質(zhì)量控制的關(guān)鍵環(huán)節(jié)
1. 原料源頭把控
從原料采購、入庫到使用,全程實施嚴格的質(zhì)量控制措施,確保原料質(zhì)量符合既定標準。
2. 生產(chǎn)過程精細化管理
制定詳盡的生產(chǎn)工藝規(guī)范與操作流程,對生產(chǎn)設(shè)備進行定期維護與保養(yǎng),確保生產(chǎn)過程的穩(wěn)定與高效。同時,加強員工技能培訓(xùn)與意識提升,確保每一道工序均能達到預(yù)期標準。
3. 成品全面檢測
對成品電纜實施全方位的性能檢測與評估,包括但不限于電氣性能、物理性能及耐候性等方面。通過嚴格的檢測手段與標準判定程序,確保電纜產(chǎn)品的整體質(zhì)量達到或超過行業(yè)要求。
4. 建立完善的質(zhì)量管理體系
構(gòu)建以預(yù)防為主、持續(xù)改進為核心的質(zhì)量管理體系。通過內(nèi)部審核、管理評審及顧客滿意度調(diào)查等手段,不斷發(fā)現(xiàn)并解決潛在問題,推動產(chǎn)品質(zhì)量的持續(xù)提升。同時,積極尋求第三方認證與權(quán)威機構(gòu)合作,增強產(chǎn)品市場競爭力與消費者信任度。

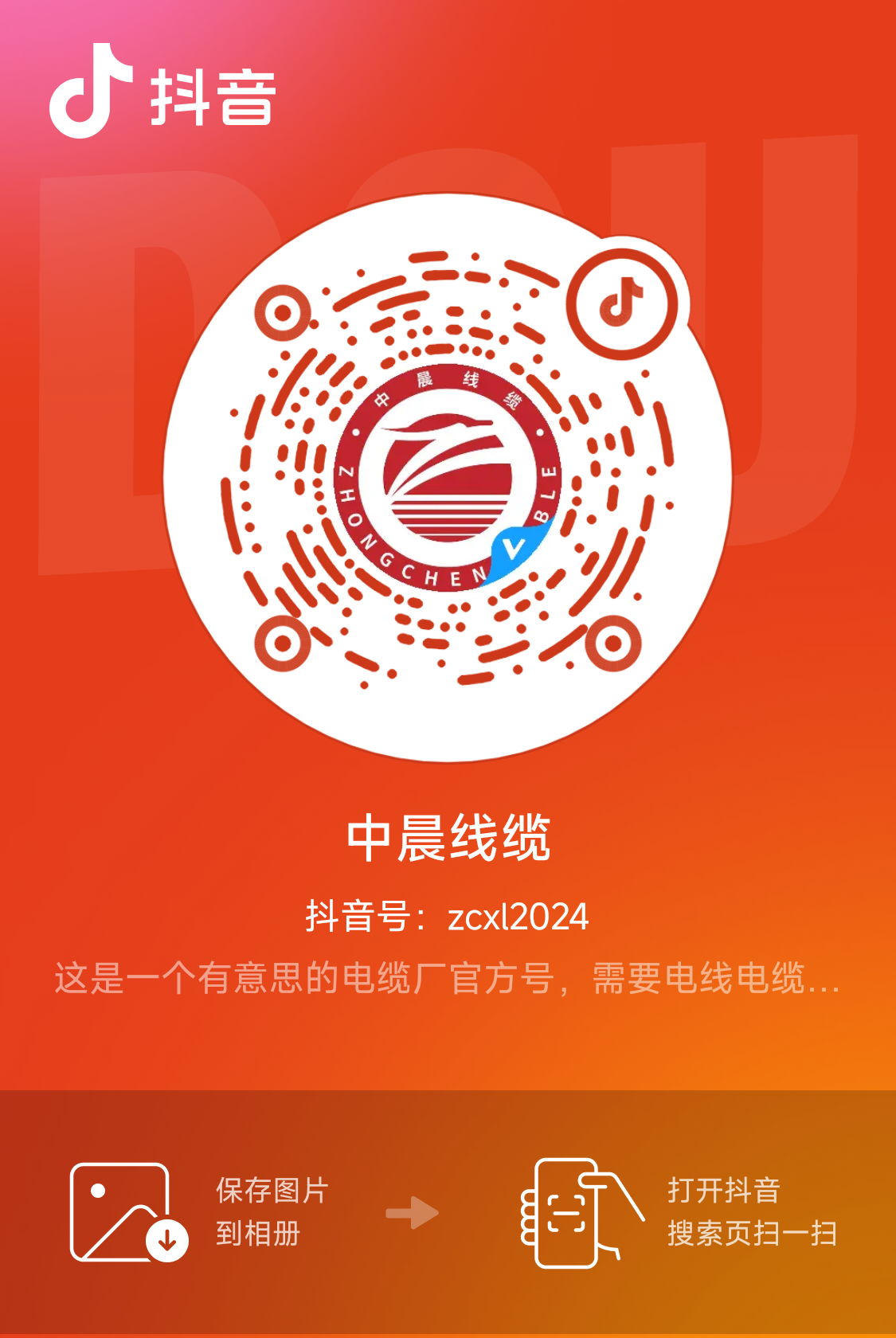
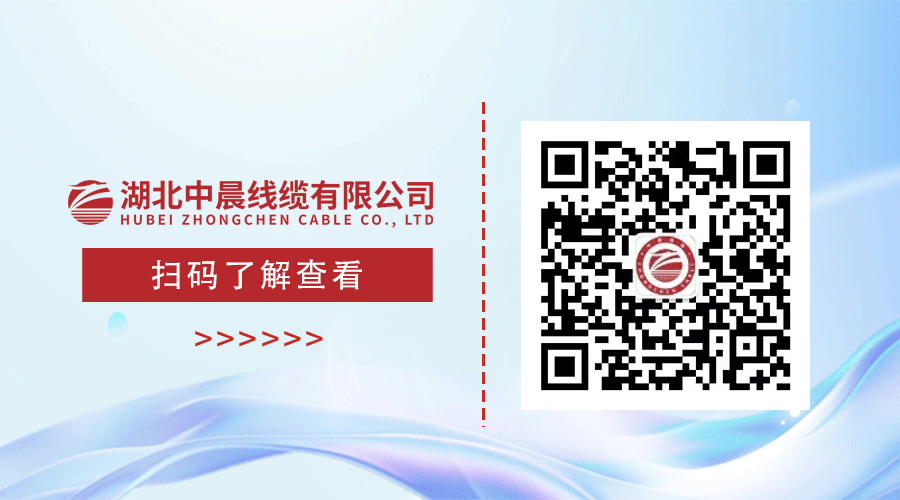